The Science Behind Porosity: A Comprehensive Guide for Welders and Fabricators
Recognizing the complex systems behind porosity in welding is essential for welders and producers aiming for impressive craftsmanship. From the structure of the base products to the intricacies of the welding procedure itself, a multitude of variables conspire to either worsen or ease the existence of porosity.
Recognizing Porosity in Welding
FIRST SENTENCE:
Exam of porosity in welding discloses crucial insights into the integrity and top quality of the weld joint. Porosity, identified by the existence of dental caries or spaces within the weld steel, is a common concern in welding processes. These gaps, otherwise appropriately dealt with, can jeopardize the structural stability and mechanical buildings of the weld, bring about potential failures in the completed product.

To detect and evaluate porosity, non-destructive testing techniques such as ultrasonic testing or X-ray assessment are typically employed. These techniques permit the identification of interior issues without compromising the integrity of the weld. By analyzing the size, form, and circulation of porosity within a weld, welders can make informed decisions to enhance their welding processes and accomplish sounder weld joints.

Elements Affecting Porosity Development
The event of porosity in welding is affected by a myriad of elements, varying from gas shielding efficiency to the ins and outs of welding parameter setups. Welding specifications, consisting of voltage, present, take a trip rate, and electrode kind, also influence porosity development. The welding technique employed, such as gas steel arc welding (GMAW) or protected metal arc welding (SMAW), can affect porosity development due to variations in warmth distribution and gas protection - What is Porosity.
Results of Porosity on Weld High Quality
Porosity formation dramatically compromises the architectural honesty and mechanical buildings of bonded joints. When porosity is present in a weld, it develops voids or tooth cavities within the product, reducing the total stamina of the joint. These gaps act as tension concentration read factors, making the weld more prone to fracturing and failure under tons. The presence of porosity also weakens the weld's resistance to corrosion, as the entraped air or gases within the spaces can respond with the surrounding atmosphere, causing deterioration in time. In addition, porosity can prevent the weld's capacity to endure stress or effect, further jeopardizing the total high quality and dependability of the bonded structure. In critical applications such as aerospace, auto, or structural constructions, where security and toughness are critical, the detrimental results of porosity on weld high quality can have severe effects, stressing the significance of reducing porosity with correct welding strategies and procedures.
Strategies to Lessen Porosity
In addition, making use of the suitable welding specifications, such as the appropriate voltage, current, and travel speed, is crucial in stopping porosity. Keeping a consistent arc length and angle throughout welding also helps decrease the possibility of porosity.

Furthermore, selecting the right protecting gas and preserving correct gas circulation rates are important in minimizing porosity. Utilizing the appropriate welding method, such as back-stepping or utilizing a weaving activity, can additionally assist disperse heat uniformly and minimize the possibilities of porosity formation. Ensuring correct ventilation in the welding setting to remove any kind of prospective sources of contamination is essential for achieving porosity-free welds. By executing these methods, welders can properly minimize porosity and create high-quality bonded joints.
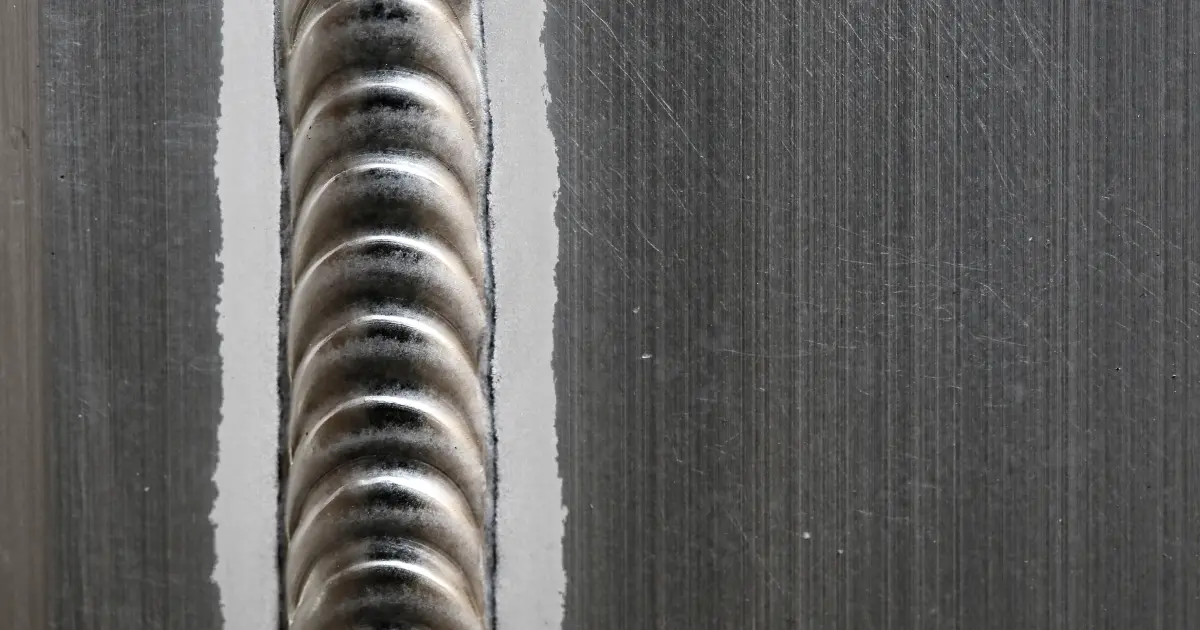
Advanced Solutions for Porosity Control
Implementing sophisticated innovations and cutting-edge methods plays a critical role in accomplishing superior control over porosity in welding procedures. Additionally, utilizing innovative welding techniques such as pulsed MIG welding or modified ambience welding can additionally assist alleviate porosity problems.
An additional innovative option includes using advanced welding equipment. Using devices with built-in functions like waveform control and innovative power resources can improve weld quality and decrease porosity threats. The execution of automated welding systems with specific control over parameters can considerably decrease porosity problems.
Additionally, incorporating advanced monitoring and assessment technologies such as real-time X-ray my latest blog post imaging or automated ultrasonic screening can assist in detecting porosity early in the welding process, over at this website allowing for immediate restorative actions. Overall, integrating these innovative remedies can substantially enhance porosity control and enhance the overall high quality of welded components.
Conclusion
In final thought, understanding the science behind porosity in welding is important for welders and producers to create premium welds - What is Porosity. Advanced services for porosity control can even more enhance the welding process and make certain a solid and reputable weld.
Comments on “What is Porosity in Welding: Common Resources and Effective Solutions”